During 2024, IT Infinity was converted at VARD Brattvåg from an older Platform Supply Vessel (PSV) into a specialized cable laying Vessel (CLV).
Dimo’s role in the project was to overhaul and upgrade deck equipment—stored ashore for 20 years—and bring this equipment back to full operation in a short timeframe.
It had to be integrated with IT Infinity’s existing hydraulic power unit (HPU), ensuring seamless operation and communication across all systems.
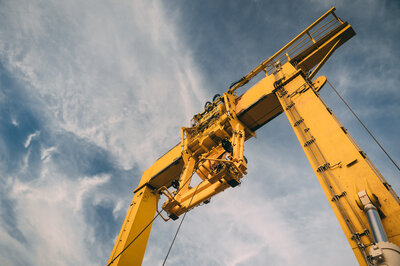
Mounted at the vessel’s stern. Used to launch and recover heavy subsea equipment or cables, providing a stable pivot point for controlled overboard operations.
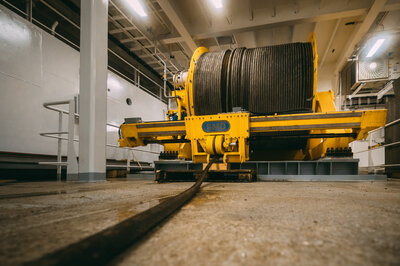
Placed below deck with a wire running up to the A-frame. Delivers pulling power or tension for towing or lifting operations, using the A-frame as the overboard guide.
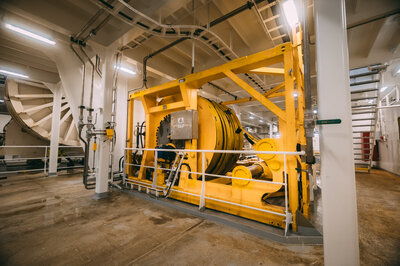
Also situated below deck, storing the umbilical cable on a large drum. Deploys and retrieves a specialized cable that provides power, data, or fluids to subsea equipment, allowing operators on the vessel to control and monitor underwater operations.
The deck equipment had been stored ashore for two decades, leading to extensive rust, water-damaged control systems, and outdated or missing components.
Hoses, valves, and sensors were no longer usable, and mechanical structures needed thorough cleaning, repair, or replacement. Several cables, brackets, and sensors were also outdated or missing.
Overall, a major overhaul was required to ensure safe and efficient operation.
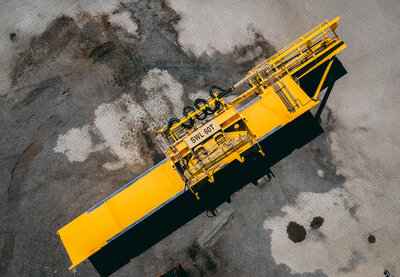
A-frame
Worn cables, hoses, and bearings were replaced, brackets and steel structures were reinforced, and a new control cabinet and control station were installed. Cylinders were pressure-tested, and leaks in valve blocks and motor gaskets were repaired.
Tow Winch
The winch was missing key piping, valves, and a functioning control system. The foundation was reinforced, new angle bars were welded on, and the spooling device was rebuilt with new brackets, bearings, and electrical components. The motor was tested for leaks, and new wiring and cable paths were installed.
Umbilical Winch
Water-damaged wiring, missing sensor brackets, and a broken drag chain were replaced. Valves were disassembled, painted, and reassembled, while hoses, cables, and junction boxes were replaced. A new control system was installed for smooth operation.
Early on, Dimo’s automation team worked closely with the crew to understand how they wanted to control the equipment.
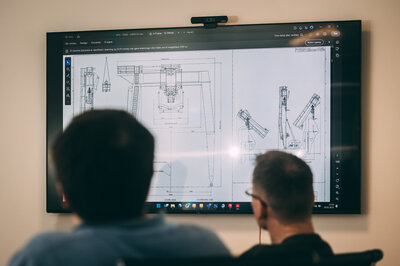
The project required an entirely new control system for the winches, enabling operators to control them from multiple locations, including local control stations and two main control consoles.
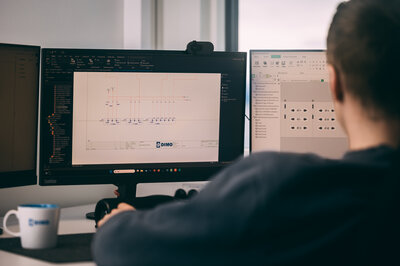
Dimo gathered the original documentation for both the vessel and the 20-year-old equipment. Engineers reviewed functional requirements from the crew and operators to design a new control system.
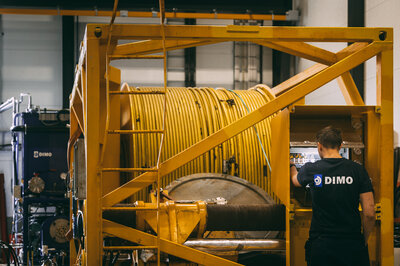
This involved creating fresh piping layouts, dimensioning hoses and valves, and drawing up new electrical schematics.
The control system needed to provide operators with real-time feedback on key parameters. This included winch load monitoring, precise tracking of cable length, and a dedicated “render mode” to ensure full control over the plow when laying cables. In addition, specialized spooling software was required to manage wire handling during operations.
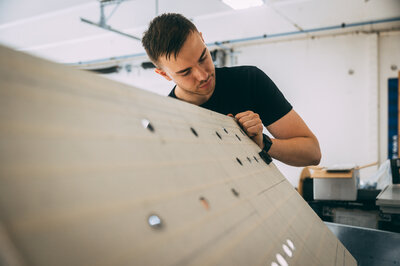
The control system needed to provide operators with real-time feedback on key parameters.
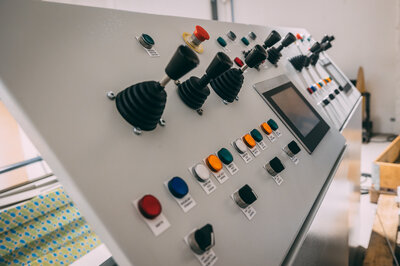
This included winch load monitoring, precise tracking of cable length, and a dedicated “render mode” to ensure full control over the plow when laying cables. In addition, specialized spooling software was required to manage wire handling during operations.
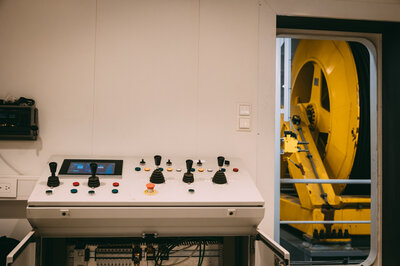
Dimo designed and built custom control panels tailored specifically for this project. The system allows operators to manage the equipment from multiple locations, including local control stations and two main control consoles.
Before the final handover, all systems were tested and commissioned to ensure reliable performance. With expertise in mechanics, engineering, and automation, and close collaboration with the crew, Dimo ensured that the winches and A-frame operate safely and efficiently.
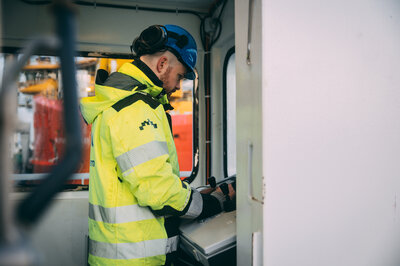
The result is a modernized, user-friendly system, ready to meet the demands of offshore operations.
Once all systems were approved, the equipment was declared ready for operations.
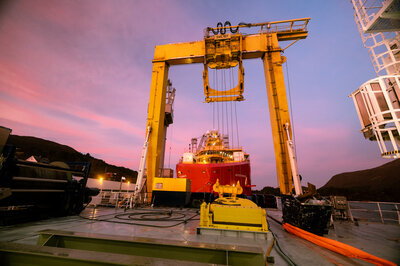
With a full overhaul, upgraded hydraulics, and a custom-built control system, the 20-year-old deck equipment is now fully operational and seamlessly integrated with the vessel’s existing systems.